(1)干式复合:溶剂型复合、无溶剂型复合;
(2)挤出复合:单层挤出复合、串联挤出复合、共挤出复合、挤出涂布复合;
(3)热溶胶复合及热溶胶涂布复合;
(4)湿式复合;
(5)热复合;
(6)特殊涂布复合:涂底胶、涂PVDC、涂PVA、涂蜡等;
干式复合是把粘合剂涂布到一种薄膜上,经烘箱蒸发掉溶剂与另一层薄膜压紧贴合成复合薄膜的方式。
挤出复合是通过挤出机将热熔性树脂从T模均匀挤出在基材上,同时与另一基材加压冷却贴合的方式,如无第二基材则为挤出涂布的方式。
湿式复合是将粘合剂涂布到一种基材上,然后与另一种基材压合在一块,再进入烘箱中蒸发掉溶剂或水份的方式。
热熔复合是对固体热溶胶加热到液态施加到基材上,通过压力使两种基材贴合在一起的方式,如无第二基材则为热熔涂布,优点是复合时间短、无溶剂、成本低,但耐热性、透明性差。热熔复合还包括蜡复合法,即把微晶石蜡热熔涂布带基材上复合。
无溶剂复合是特殊的干式复合,把无溶剂的粘合剂施加到一种基材上与另一基材在压力下贴合在一起的方式。
热复合是把涂布了热合涂层的一种基材加热后与另一基材加压贴合在一起的方式。
广义的复合还包括各种涂布方式,真空蒸镀金属及金属氧化物、共挤流延膜、共挤吹塑薄膜等。
主要复合方式的特点见表1,各种复合工艺特点比较见表2。
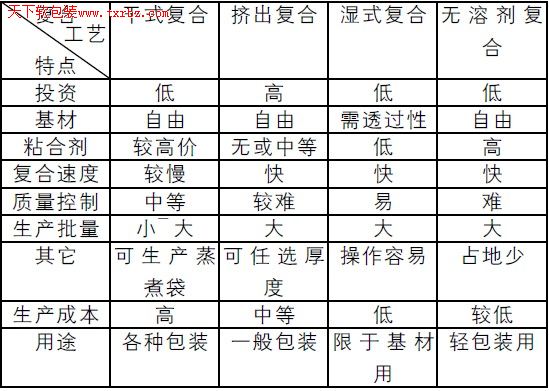

2、挤出复合的机理
挤出复合是将热熔性树脂,如PE、EVA、EAA等,由塑料挤出机熔融塑化后由T型模头挤出在一种基材上,同时与另一基材复合贴压在一起,冷却后制成复合薄膜的方法。
挤出涂布是热熔性树脂连续均匀地挤出,在一种基材上直接冷却收卷成复合薄膜,不与第一基材贴合的工艺。实际中,往往把挤出涂布归为挤出复合,并不特别列出。挤出复合目前主要有三种方式,即单层挤出复合、串联挤出复合及共挤出复合
挤出复合是将PE等热塑性树脂作为粘合材料使用,将挤出的熔融树脂薄膜与复合基材加压贴合在一块,使界面处的分子互相穿插结合,将基材粘合起来。粘合是被 粘物与粘结剂接触后分子间作用力的结果,有时两者还发生了化学反应。粘结的另一个条件是粘结料必须流动性好,可以浸润被粘物表面。
PE是如何完成这一任务呢?PE分子比较规整,分子极性很弱,是非极性材料,在200℃左右的普通加工温度下,是难以与其他材料粘结的,当PE在300℃以上的高温下,其熔体易在空气中氧化,产生极性,并使熔体有足够的流动性、浸润性和铺展性。
PE熔体在300℃以上的模头中挤出时,在高温空气流中,表面发生氧化。这种热氧化过程是自由基反应历程:
链引发 HR→ H·+R·
HR....R′H → HR·+HR′·
HR+O2 →R·+HOO·
链增长 R·+O2 →ROO·
ROO·+RH→ ROOH+R·
ROOH→RO·+HO·
2ROOH→RO·+ROO·H20
RO·+RH→ROH+R·
表面热氧化引入了大量基团,如羰基、羟基、羧基等,还因脱氢形成不饱和双键。极性基因的引入增加了表面间相互作用和与其他材料表面的作用力。分子链的断裂降低了表面分子量,降低了玻璃化转变温度和粘度,促使了界面流动和扩散。因此,PE的粘结性大大提高了与其他材料复合的目的。
3、挤出复合的优势
与其他复合方式相比,挤出复合有其独特的优点。共挤出复合的主要特点是:多层薄膜一次挤出成型,其工艺简单,节省能源,生产效率高,且成本低;复合薄膜柔软,手感舒适;因层与层之间无需使用粘合剂,所以不存在残留溶剂问题,薄膜无异味。
3.1复合速度快,适合大批量生产,生产效率高,最快可达1000m/min的高速。
3.2可自由选择基材。可代替干式复合薄膜或减少干式复合的次数,更具有环保节能的特点。通过调整阻隔层的厚度及多种阻隔材料的搭配使用,可以灵活地设计出不同阻隔性能的薄膜,还可灵活更换调配热封层材料,满足不同包装的需求。
对于不同食品的包装要求及包装设备,还可以调节热封层的材料来满足:
(1)EVA 低温热封
(2)m-LLDPE 抗污染热封性
(3)EAA 油类制品的热封
(4)Surly 贴体性、抗污染热封性,抗介质。
3.3加工成本较低,省去了一道热封膜生产工序,粘合剂使用极少。多层共挤复合工艺使用多种不同功能的树脂,只采用一道工序即可制成具有多功能的复合薄膜制品,可降低生产成本。并且,还可在满足客户使用要求的前提下,将所需性能的树脂原料减至最小厚度,单层最薄可达2~3μm,可大大减少昂贵的树脂使用量,又降低了材料成本。
3.4结构灵活
可任意设定挤压厚度。多层共挤技术可将多种原料进行不同组合的搭配,充分利用不同性能的原料,一次成型,不受市场相关产品规格的限制,有效地满足不同包装场合的需要。层次越多,结构设计越灵活,成本越低。可一次性连线生产多达9层的复合材料,还可生产发泡膜和微孔膜等。
3.5产品用途广泛
多层共挤复合材料制品可以涵盖几乎所有的包装领域:食品、日化产品、饮料、药品、保护膜甚至航空航天产品等,目前许多干式复合材料制品在国外都已采用共挤复合工艺。干式复合工艺无法生产的软管、纸塑铝复合产品、航空航天等产品也都是采用共挤复合工艺来实现。适合卡纸、无纺布、编织布的复合。
3.6共挤挤出复合优点突出
通过两台或两台以上挤出机,将熔融的塑料分别挤到共分配器和一个T模头,再涂布到基材上压合冷却,一层为粘结树脂,另一层为热封材料,根据不同的基材采用不同的粘结树脂。特点主要有:①没有任何毒性,没有任何危害。②没有残留溶剂。③没有废气污染。④无干燥箱,能源消耗少。⑤生产成本较低,挤出粘接层厚度小。⑥复合的剥离强度很高,通常可达3N/15mm以上,甚至无法剥离。对剥离强度要求很高的产品,用特殊的热粘性树脂进行复合,剥离强度可达4N/15mm以上。
3.7挤出复合的卫生安全性好
有些基材通常底涂增粘的AC剂,经烘箱干燥进行贴合。
底涂的AC剂有:以醇类溶剂为主的水性AC剂和以醋酸乙烯溶剂为主的溶剂型AC剂,
(1)AC剂涂布量小,残留极少 ;由于使用AC剂非常少,排废对环境污染不大。
(2)由于共挤复合中不使用AC剂,不存在粘合剂的安全性及溶剂残留问题,使食品安全卫生得到了极大的保障,是其他任何复合方式所无法比拟的。
4、主要挤出复合工艺
4.1 单联挤出复合工艺
单联式挤出复合机由一台挤出机和复合装置组成,可涂布复合二层结构,也可夹心复合三层结构。
4.2串联挤出复合工艺
串联式挤出复合机由一台以上挤出机和复合装置串联排列组成,可复合四层以上结构。
4.3 共挤复合工艺
共挤出复合机由两台或两台以上挤出机,将熔融的塑料挤到分配器和一个T模头挤出复合。
4.4 组合式挤出复合工艺
把单联挤出、串联挤出、共挤复合共同集为一体的方式。主要的排列方式有1-2、2-2、2-2-2、2-2-1等,再加上翻转及上胶装置,提供了极大的灵活性,可一次性生产结构复杂的产品。
4.5增粘工艺。因PE粘接树脂与基材的粘合牢底较低,因此。在挤出复合中常需要采取增粘措施,以增加挤出复合材料的粘合强度。常用的增粘方法有以下几种:
①电晕处理。在复合前对基材表面进行电晕处理是最常用的措施。
②打底处理。复合前在基材的表面预涂布一层增粘剂。
③高温氧化。在热融片膜从T型模头的出口流到复合基材上的流下距离中进行空气氧化。
④臭氧氧化。是采用臭氧发生器进行氧化,保证了粘接树脂与基材间的粘合。这样允许在较低的挤出温度下进行挤出复合,不会产生PE的气味问题。另外,热熔片膜另一面上的氧化程度较低,也使其热封性能得到了改善。
⑤火焰处理。在许多PE与纸基的挤出复合中,对纸基表面进行火焰处理,即使其表面暴露于火焰的直接喷冲之下,这样能使PE与纸基的粘合性得到改善。
5、挤出复合的发展趋势
挤出复合设备的发展趋势是要朝着组合结构、专用化、系列化、标准化、复合化、微型化、大型化、个性化、智能化方向发展,同时要满足节能、节材、高效的要求。
挤出复合用粘结性树脂和热封合树脂不断改进和发展,极大地扩大了挤出复合可生产的品种和性能。为了实现多层结构的产品,多层共挤复合用塑料树脂也在不断推出,除常用的LDPE、PP各种热粘结树脂外,还在向其他热塑性树脂方向发展,预计在不久的将来,挤出复合专用的LDPE、LLDPE、PS、PA、PC、PVA、EVOH、PVDC等功能性树脂能够大规模生产时,多层共挤复合薄膜材料将会有更大的发展。
(1)面对包装产品向多品种、少批量的方向发展,节约资源、提高效率已成为趋势,挤出复合设备向自动化、数字化、智能化方向发展。如,快速自动调节清洗的模头,厚度自动测量装置,遥控生产控制系统等。
(2)共挤技术不断发展。共挤技术可以生产特殊的功能膜,可减少生产流程,一次性生产出多层薄膜。不需溶剂和AC剂,可降低成本,减少昂贵树脂的使用。总之,共挤的发展适应了减少生产周期、节省资源、增加附加值的需求。
(3)连线生产设备不断发展。综合性的生产线越来越多,与印刷相组合、与干、湿法复合相组合、与底涂上光相组合等,加工共挤复合、串联挤出复合,可一次性生产具有非常复杂结构的产品,尤其用于医药包装、高阻隔产品、调味料包装、牙膏包装上。
(4)设备大型高速化
设备的大型化、高速化可以降低生产成本,提高生产效率,也是市场的需求。如无菌包装材料、托盘片材、皮革离型纸的生产,要求大卷径、大幅宽,织物涂覆达4.5m宽。
(5) 高速、高产化
挤出机高速、高产,可使投资者以较低的投入获得较大的产出和高额的回报。但是,挤出机螺杆转速高速化也带来了一系列需要克服的难点:如物料在螺杆内停留时间的减少会导致物料混炼塑化不均,物料经受过度剪切可能造成物料急骤升温和热分解,挤出稳定性控制困难会造成挤出物几何尺寸波动,相关的辅助装置和控制系统的精度必须提高,螺杆与机筒的磨损加剧需要采用高耐磨及超高耐磨材质,减速器与轴承在高速运转的情况下如何提高其寿命等问题都需要解决。
(6)辅机配置高能化
除了主机外,附属的配置齐全及性能高已是趋势。如红外分层测厚仪、自动模头、在线混配、火焰处理、臭氧处理等。
(7)智能化和网络化
发达国家的挤出机已普遍采用现代电子和计算机控制技术,对整个挤出过程的工艺参数如熔体压力及温度、各段机身温度、主螺杆和喂料螺杆转速、喂料量,各种原料的配比、电机的电流电压等参数进行在线检测,并采用微机闭环控制。有的公司己采用网上远程监测、诊断和控制,对挤出成型生产线进行网络控制。这对保证工艺条件的稳定,提高产品的精度都极为有利。