长期以来苯类溶剂尤其是甲苯以其适中的干燥速度、通用的溶解能力以及能提高色浓度的折光率成为软包装行业中最常用的溶剂。软包装产业链上的企业尤其是油墨制造企业与印刷企业的生产车间和实验室内的仪器设备、管道甚至空气中都残留着大量苯类溶剂,企业要将产品的苯类溶剂含量控制到“不能检出”绝非简单地停止使用苯类溶剂就能够实现的,要想控制软包装产品苯类溶剂的残留就必须在产品生产的每一环节都严加防范。
一、原材料的控制
无论是重金属含量、卤素含量、多环芳烃含量这些我们接触时间较长的受控物质,还是这次的苯类溶剂含量控制,对原材料的严格控制是最重要、最有效也是最便捷的手段。
对于油墨生产企业,主要关注的原材料有颜料、合成树脂、助剂及有机溶剂。基于粉状颜料的生产工艺,粉状颜料一般不含苯类溶剂,而切片颜料及色浆则很可能会含有甲苯、二甲苯这两种溶剂,油墨生产企业应对现用的切片颜料及色浆进行检查评定,在无苯油墨中停止使用含苯颜料,尽快寻找其替代品。合成树脂及助剂一般都在有机溶剂中溶解后以液态性形式加入油墨中,油墨生产企业应要求上游供应商提供非苯溶性的树脂及助剂,测试其在无苯类溶剂状态下的溶解性后投入无苯油墨生产中。相对于颜料、合成树脂及助剂以跟换原材料的方式来控制苯类溶剂含量,要控制有机溶剂中苯类溶剂的含量则主要依靠完善的预防措施及较强的检测力度。企业的原材料检验部门应对每一批可能在无苯油墨中使用的有机溶剂进行色谱分析,一旦检出苯类溶剂(超过公司检验规格)或纯度未达标都应坚决退回,要求供应商更换。
对于软包企业,除了要关注印刷油墨、有机溶剂还要对印刷薄膜、胶粘剂也进行严格控制。
二、无苯车间的建设
如前所述,在现阶段即使不使用苯类溶剂和其他含苯原材料也很难实现GB/T10004-2008中规定的“苯类溶剂不得检出”。其原因就在于经过了长期的含苯生产,油墨生产企业制造车间和软包企业印刷车间内的设备、管道、空气中都大量残留着苯类溶剂,在这个环境下制造出来的产品想要不含苯类溶剂是极困难的。我们可以通过实验来了解生产环境对软包装产品溶剂残留的影响:在一卷BOPP(双向拉伸聚丙烯)薄膜上裁下3份相同面积的薄膜,分别放置在室外、实验室内(常进行含苯类油墨实验)和盛有甲苯的敞口的容器旁,10日后测试3份薄膜的溶剂残留水平。测试结果见表1
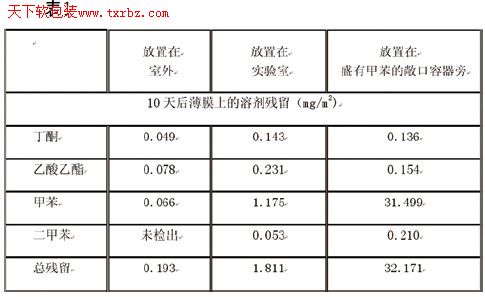
实验结果显示仅空气中的苯类溶剂吸附在印刷底材上一个因素,就会导致苯类溶剂残留远远超过新标的限定,甚至造成总残留也超标。由此可见,制造一个无苯的生产环境对制造出符合新标限定的软包产品意义重大。
建设一个无苯车间可以通过更换管道、彻底清洗仪器设备(使用酯类溶剂,如:醋酸乙酯)对原有的含苯车间进行改造。除了硬件上的投入,企业还需要对现场管理及操作人员进行培训,不可在生产繁忙时将无苯产品转移到含苯车间生产,更要坚决杜绝将含苯产品转移到无苯车间生产。交错生产带来的苯类溶剂污染很可能会导致最终产品无法达到“苯类溶剂不得检出”,致使花费大量人力物力建设的无苯车间变得毫无意义。
有些企业提出在无苯车间生产,仍然觉得“味很难闻”甚至比含苯车间气味更重。如何解答这一问题?
应当指出,“无苯车间”并非“无气味车间”。苯类溶剂作为芳香烃类化合物,其气味并非比一些非苯类有机溶剂强烈;而一些比苯类溶剂气味更小的有机溶剂其有害性也可能远远高于苯类溶剂。以表2中的3种有机溶剂为例:甲醇是一种本身无特殊气味的有机溶剂,然而它属于中毒类化学物质,可引起脑水肿、双目失明等严重健康危害;丁酮(甲基乙基酮)是无苯生产时一个常用的溶剂,其气味比甲苯更为强烈,而它对人体的危害远远小于甲醇和甲苯。当然,这样比较的目的并不是为了给某些有机溶剂正名,而是要明确对待化学品不能因其气味强烈而认定其危害大,更不能因其气味小或无气味认定其无害这个观念。
虽然无苯车间无法到达“无气味”,但能明显降低产品的苯类溶剂残留并能改善现场人员的工作环境。
总之,软包装企业想要早日达到残留溶剂总量≤5.0mg/m2、苯类溶剂不得检出(即<0.01mg/m2)这一标准,建设一个无苯车间刻不容缓。
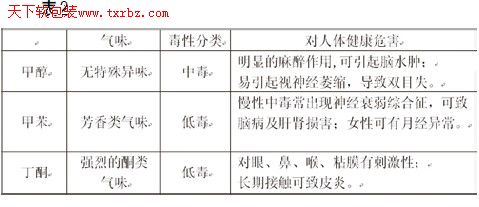
三、检测水平提高
既然新标限制的是软包装产品的溶剂种类及残留量,若是软包装商业链上的企业没有熟练掌握产品溶剂残留的检测方法,那如何知道自己的产品是否合格?随着无苯产品在企业内比重增加,与其每个产品都委托其他公司代检,不如自己来掌握检测方式。
现阶段,国内最常用的是气相色谱检测产品溶剂残留。色谱法的分离原理就是利用待分离的各种物质在色谱柱中的分配系数、吸附能力等亲和能力的不同来进行分离的。
气相色谱法检测软包装产品的溶剂残留是使用载气使含有混合溶剂的气体通过色谱柱,使气体中的各溶剂与色谱柱内的物质发生相互作用。由于各个溶剂在性质和结构上的差异,与色谱柱内的物质产生的作用力的大小、强弱不同,使得各溶剂被色谱柱保留的时间不同,从而按一定次序由色谱中先后流出。与适当的柱后检测方法结合,实现混合物中各组分的分离与检测。
软包装企业在检测产品溶剂残留时主要遇到的是以下几个难点:
一是没有仪器,二是有仪器不会操作,三是会操作不会分析。
对于仪器的选择,由于新标中“不得检出”的严格要求,必须选购对苯类溶剂最低检出限不低于0.1ppm的气相色谱仪。另外,为了减少人为因素对试验结果的影响,应采用顶空设备或自动进样器来注入待测产品。
许多企业都遇到过一个同样的问题。就是当原本一台仪器(不单指气相色谱仪)的操作人员离开企业后才发现企业内没有懂得如何操作这台仪器的人员,导致这台仪器长期废置或无法正常工作。为了避免此类尴尬的情况出现,企业应多培养气相色谱仪的操作人员,使操作人员之间能相互学习提高。对于仪器供应商提供的相关培训也应积极参加,增强对仪器的认识。
前文提到过气相色谱仪是通过各溶剂在性质和结构上的差异来进行分离与检测的。因此,会出现个别几种溶剂的保留时间(出峰时间)相近的情况。例如:甲苯与甲基异丁基酮(4-甲基-2戊烷),二甲苯与丙二醇甲醚醋酸酯的保留时间极为接近(相差零点几秒)。而甲基异丁基酮与丙二醇甲醚醋酸酯都是在无苯生产时可能会添加的辅助溶剂,一旦检测时与苯类溶剂混淆,必然造成产品苯类甚至总残留的超标。而由检测分析错误造成的“苯类溶剂超标”会导致企业从原料到生产操作复查遍都无法寻找到产品苯类溶剂超标的原因。
如果说原材料的控制、无苯车间的建设是企业针对新标在硬件上的投入,那么溶剂残留检测水平的提高则是企业必须重点投入的软件设施。
四、结语
当前,软包装产业链上的企业正迎来一场国家标准的洗礼和考验。有些企业认为新标过于严格,但是既然这些标准已经通过了国家有关部门的审核并正式推出,就要相信它在技术上的可行性。如果出台的是所有企业都能达到的标准,那出台新标准还有什么意义?新标准的出台对我国软包装企业是挑战也是机遇,它促使了国产食品包装更为环保,使我国食品及食品包装能与国际标准接轨。能生产出符合新标产品的企业就能占据更大的国内市场,进一步拓展海外市场,参与全球化竞争,让更多的“中国制造”出现在国外的食品柜台上。