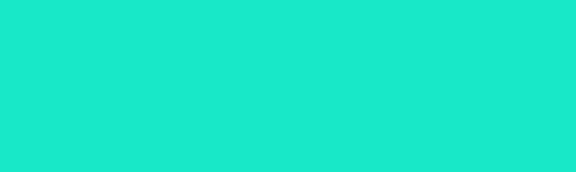
楼主
软包装杂工-发帖时间:2025/2/27 8:58:37近年来,无溶剂胶粘剂的应用逐渐扩大,正逐步取代传统的溶剂型胶粘剂。在多种需求中,PET.ink//AL材料结构的需求逐渐显现,成为行业人士关注的一个重要问题。在处理这种材料结构的复合时,我们面临两个主要挑战:
1、外观控制:如何有效消除白点并防止其再次出现;
2、背透问题。本文将重点分析这两个问题的成因及解决方案。
许多人在思考铝箔的表面处理为何如此复杂。普遍认为,铝箔等硬质材料具有较强的刚性,这使得在复合过程中对复合线压力的要求更高。那么,是否仅仅提供足够的复合线压力就能解决这个问题呢?首先,我们要分析影响复合线压力的几个因素。1. 复合胶辊的硬度:大多数橡胶辊的邵氏硬度约为75度,经过实测,在70至75度之间的较为常见,而硬度≥80度的则相对较少。当加热复合钢辊后,复合辊的温度会通过热传导影响复合胶辊的硬度,使其进一步降低。同时,若截面积增加,复合线压力也会随之下降。在这种情况下,不同的杠杆形式和气缸规格都会对复合辊的形变产生显著影响,而硬度较低的复合压辊则可能导致复合线压力不足。
2. 材质厚度的影响:以PET(12μm)和铝箔(6.5μm至9μm)为例,外层材料的厚度相对较薄,且材质的刚性较强。通常,铝箔在复合时置于第二道工序,为了保证生产效率和材料的平整度,施加在铝箔基材上的张力不会过大,并且会尽量缩短物料的行走距离。然而,不同设备型号使铝箔进入复合辊的角度存在差异,这一点对复合后的外观有显著影响。值得强调的是,不同的包角设置对PET/AL这类“刚性”材料的影响尤为明显,容易在压合后出现气泡。
3.复合后的外观质量至关重要:如果线压力不足,不能有效排出夹在薄膜之间的空气,那么在收卷环节就可能出现问题。通常建议复合机的复合压力不低于1000kgf/m。通常,新装配的设备能够轻松达到这个标准,而问题多出现在使用时间较长或者维护不当的设备上。空气压缩机及其相关组件的老化,会逐渐导致复合压力降低。这一问题常被很多企业忽视,常常在出现白点后才开始寻找原因。经过一番奔波,却未能找到真正的问题所在,反而对此事感到困惑,此时容易误入歧途,反复纠缠于其它原材料或操作细节,甚至有些会过于钻牛角尖,进而影响正常生产。
此外,采购的设备及其部件如果本身就未达到相应的压力要求,那就属于先天性缺陷。在我走访众多彩印企业时,发现一个现象:在处理不同厚度和材料的复合时,相当一部分设备在操作过程中并没有调整复合压力(不论是干复合、无溶剂复合、湿法复合还是涂布机等)。这种固定的“规定”并不意味着无法使用,其缺点也是非常明显的。在较宏观的层面上,单一参数的设定可以涵盖更多应用场景,但在具体的材料结构组合上则可能出现细微的差异。例如,在目前被广泛认为较为复杂的复合PET//AL材料结构中,原有的复合压力是否合适需要认真审视,希望这一点能够引起彩印企业生产人员的关注。根据我目前接触到的各种设备型号和品牌的经验,在复合PET//AL时,复合压力的设置至少应在3.5bar以上。
铝箔的特殊性体现在以下几个方面:1. 表观特性:铝箔作为一种高反光材料,其影像映射能力十分强,因此复合后容易出现“镜像”光学效果,放大复合、印刷甚至原材料上存在的表观缺陷。因此,对粘接界面的“细腻”程度要求非常高。同样,镀铝涂层的情况也类似,其高反光镜面效果更加明显。因此,如果能够将粘接界面处理得更细腻,将显著降低PET//VMPET材料结构的外观控制难度。
2. 双层基材的表面张力差异:PET的表面张力在52~58达因之间,印刷油墨的表面张力约为40达因,而铝箔的表面张力则超过850达因。
复合材料的国家标准(GB10570-89)规定的表面张力要求不得低于72达因。而胶粘剂的表面张力大约为42达因。三种材料的表面张力差异越大,就越可能导致复合面在两侧材料接触时产生微观运动的不一致,尤其是在油墨印刷后,表面张力较低的情况下,往往会出现生产后没有白点,而在熟化阶段逐渐出现白点的现象。此外,胶粘剂在反应过程中会产生内聚力,这是所有胶粘剂产品的内在特性。那么,如何妥善应对这一问题呢?
这就对涂布界面提出了更高的要求。我们需要关注胶粘剂的流平性以及设备上各个转移界面的光滑程度对涂胶量和转移界面效果的影响。无溶剂涂布工艺采用光辊转移,从承胶辊到基材总共进行四次转移。在第一次转移后,每次转移的前载胶面表面状态都会直接影响后载胶面的附着效果。在这个逐步的过程中,胶层逐渐变薄,载胶面表面状态的影响显得愈加明显。同时,不同胶粘剂在流平性方面也存在细微差别,这些差别会逐渐放大到最终的载胶膜上。
再次强调,干复和无溶剂胶粘剂在二次流平性方面有显著差异。很多人在进行干复时通过熟化来解决复合白点的问题,但在无溶剂复合时,干复的经验无法直接应用。
总体而言,提升设备各个转移接口的光滑度,对于所有复合产品的外观都是有益的。关于水分对无溶剂胶粘剂的影响,主要涉及在复合后熟化阶段出现的气泡问题。这一现象在业内有一个普遍的看法,认为水分与胶粘剂中的-NCO反应会产生大量气体,而由于聚酯和铝箔的优良阻气性,导致气体无法充分释放,从而在两层材料之间积聚形成气泡。然而,这一理论存在一个无法解释的问题:在PET//VMPET或PET//PET等高阻隔材料的复合中,为什么这个问题并不明显?
我们来分析胶粘剂与水分反应的过程,并进行量化。理论上,胶水与水的反应会生成气体。假设1克某种纯预聚体需要0.006克水,生成0.0015克二氧化碳,这在数量级上差异达10²。从实际生产情况来看,PET//AL的卷材通常比较紧密,因此无论是气体的生成速度还是生成量,都不会是熟化阶段出现气泡的主要原因。实际上,在压卷状态下,这些气体会被挤压并从复合膜的边缘排出,且这些气体的产生是随着胶粘剂的逐步反应而逐渐释放的。
根据上述公式的理论值,在实际操作中,不可能有如此“大量”的水分参与胶粘剂的反应,并且主剂与固化剂是同时反应的,因此不可能所有的-NCO都与水反应。那么,气体出现白点现象是否有可能呢?答案是肯定的!主要原因有以下两点:
(1)印刷溶剂的残留通常在超标的情况下,油墨层中的有机溶剂在熟化室加热后会迅速释放,此时单位时间内的浓度非常高,汽化膨胀后的溶剂会显著影响外观。
(2)很多人现在关注印刷油墨层的微观表面细腻程度,这也可以作为参考,帮助解释其他材料中气体引发气泡的原因。在生产过程中,实际产生的气泡数量远低于理论值。
许多人在尝试无溶剂复合PET.ink//AL时,会遇到背透现象,某些干复生产过程中也可能出现这种现象。各行各业都在借助自身的专业力量来攻克这一难题,例如不同的设备制造商通过各种思路和方法在生产过程中进行探索。而我们作为胶粘剂生产企业,则通过改进胶粘剂产品来解决这个问题。
在这里,我想提供一些微观层面的情况供大家参考:胶粘剂在铝箔材质上出现透过现象与多个因素有关。一方面,与铝箔的质量或状态直接相关,铝箔上针眼的大小和数量都是显而易见的。另一方面,与胶粘剂的粘度有关。
众所周知,流体的粘度越低,流动性越佳,而胶粘剂的粘度阈值正好包含了能够穿透铝箔针眼的临界值。因此,我们需要研究如何干预这一因素,使其在发生穿透之前,粘度达到临界值以上,这样就能够有效解决铝箔的背透问题。
尤其是对于无溶剂型胶粘剂,双组分的粘度变化过程及其对应关系与溶剂型胶粘剂有所不同。单组分无溶剂胶粘剂由于其独特的粘温曲线和较高的粘度,使得铝箔材质复合相对简单。而干式复合经过多年的实践,具备了一定的物理条件,因此在铝箔材质上的复合难度大为降低。因此,通过干复经验指导无溶剂操作工艺存在一定片面性。
无溶剂胶粘剂在使用时,其胶体的粘度通常较低,但反应速度却相对较快。这意味着其反应程度与粘度呈反比关系,并且在短时间内会迅速变化。我们知道,背透现象的主要原因是胶粘剂的粘度阈值涵盖了可穿透与不可穿透的临界点。因此,如果能够有效干预粘度的变化,就能够避免背透的发生。
一般而言,无溶剂胶粘剂的盘寿命大约为30分钟,此时胶粘剂的粘度较低,但反应速度较快。在这个阶段,如果能够迅速有效地提升胶粘剂的粘度,那么就能够显著减少甚至消除胶粘剂通过铝箔针孔的现象和程度。复合膜是多种因素综合作用的结果,但选择高粘度的无溶剂胶粘剂并不一定能保证产品质量。需要指出的是,绝大多数高粘度的无溶剂胶粘剂在操作和清洁等环节存在不足,使用上不够方便。
此外,为了确保高粘度无溶剂胶粘剂的流平性,往往需要在较高的操作温度下进行,以控制涂胶量并确保复合表面不出现白点。然而,在这种温度下,高粘度无溶剂产品的实际粘度并不高。因此,所谓高粘度无溶剂产品的“高”并不与我们所需的高粘度在同一层面上。
|
- ·有办法!无溶剂复合多种常见不良现象及解决[7-21
- ·揭秘:无溶剂与干式复合机的五大核心区别[6-7
- ·铝箔袋复合时出现麻点、波浪鱼鳞片、丝纹、蘑[4-16
- ·无溶剂胶粘剂使用的三大难题及解决办法![4-10
- ·无溶剂复合的工艺,不注意这几点等于白干![3-31
- ·无溶剂复合在药品包装用复合膜上的应用实践![3-20
- ·无溶剂复合白点气泡问题解决攻略[3-5
- ·无溶剂复合中镂空图案与镀铝白点问题的解决方法[3-3
- ·厉害!无溶剂复合PET//AL工艺技术难点[2-27
- ·铝箔复合袋剥离强度问题及解决策略,高温高湿环[2-19
公众号 客服
微信